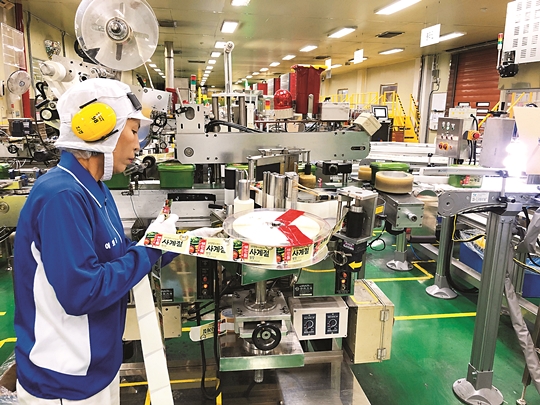
된장을 퍼서 용기에 담은 뒤 밀봉하고 라벨을 붙이는 식의 작업이 사람 손을 떠난 지 오래다. 지난 20일 충남 공주 계룡면에 위치한 CJ제일제당 공주공장에서 살펴본 공정도 마찬가지였다. 정량의 장류 제품이 담긴 용기는 컨베이어 벨트를 따라 움직이면서 차츰 시판되는 모습을 갖췄다. 뚜껑을 닫고 라벨을 붙이는 건 물론 박스 포장까지 사람 손이 필요한 일은 거의 없었다. 간간이 불량이 난 제품이 생산 라인 옆으로 밀려 나오면 근로자들이 확인하는 게 전부였다. 110여명 남짓한 인원으로 하루 100여t에 이르는 완제품을 생산해낼 수 있는 비결도 자동화다.
그렇다고 사람 손이 아예 필요 없는 것은 아니다. 자동화된 장비들이라도 기계다. 오류가 날 수 있다. 이를 바로잡는 업무는 사람의 손에 맡겨진다. 사고 위험이 가장 큰 지점도 이 때다. 사람이 작업을 하는 동안 멈춰 있어야 할 기계가 돌아가면 인명 피해로 이어진다. 지난해 12월 컨베이어 벨트 협착사고로 사망한 하청업체 근로자 김용균(당시 24세)씨 사건의 발단도 이러했다. 생산성과 효율성을 높여주는 자동화 설비가 인명을 위협하는 흉기로 변하는 건 한순간이다.
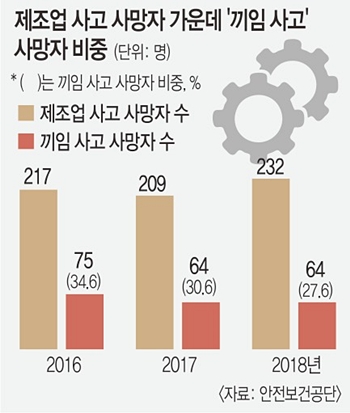
줄지 않는 ‘끼임 사고’
어느 제조업 현장이나 ‘안전’을 강조하지만 사고는 끊이지 않는다. 23일 안전보건공단에 따르면 지난해까지 최근 3년간 제조업에서 발생한 사고 사망자는 658명에 이른다. 이 가운데 ‘끼임 사고’라는 특정 유형의 사고 비중이 높다. 2016년 전체 제조업 사고 사망자(217명) 가운데 34.6%(75명)는 끼임 사고가 원인이었다. 지난해 끼임 사고의 사망자 비중이 27.6%로 다소 줄었지만, 이는 전체 제조업 사고 사망자가 늘면서 상대적으로 비중이 줄었을 뿐이었다. 최근 3년간 끼임 사고에 따른 사망자는 60~70명 수준을 오르내렸다.
인명 피해가 이어지자 정책은 변해왔다. 김씨 사망 사고 이후 ‘김용균법’으로 불리는 개정 산업안전보건법이 지난해 12월 국회를 통과했다. 산업재해가 빈번하거나 사고 가능성이 높은 업종은 외주를 줄 수 없도록 만드는 게 핵심이다. 내년 1월 1일 시행되는 개정 산업안전보건법 58조는 도금작업 등 고위험군으로 분류되는 작업의 하도급을 금지했다. 이와 함께 사업주와 하도급업체 대표의 처벌도 강화했다. 근로자 사망사고 발생 시 사업주에게 부과하는 벌칙(7년 이하 징역 또는 1억원 이하 벌금)에 가중처벌이 가능토록 했다.
다만 법 개정만으로 위험이 사라질지 미지수다. 위험한 업무를 외주에 맡기지 않는 만큼 안전에 만전을 기할 수는 있다. 그렇다고 사망사고 ‘0%’를 장담할 수 없다. 아무리 안전을 강조해도 단순한 오작동 하나로 사고가 발생할 수 있기 때문이다.
‘악순환 고리’ 끊어야
현장 전문가들은 아예 사고 발생의 싹을 잘라야 한다고 입을 모은다. 복잡한 자동화 설비를 갖추고 있는 CJ제일제당 공주공장의 경우 여기에 집중했다. 공주공장은 충남에 있는 CJ제일제당 공장 4곳 가운데 2번째로 규모가 크다. 2009년 이후 단 한 건의 안전사고도 발생하지 않고 있다.
하루에 120~150t에 이르는 된장·쌈장을 생산하는 공주공장의 안전 비결은 ‘투명 덮개’다. 지난 20일 하얀 위생복과 위생 모자를 쓰고 공주공장 현장에 들어가자마자 복잡한 컨베이어 벨트 라인과 함께 수많은 설비를 마주했다. 자칫 손을 잘못 넣기만 해도 끼일 수 있는 장비들이었다. 그런데 공주공장에선 그럴 일이 없다. 위압적으로 보이는 설비와 컨베이어 벨트 겉에는 투명한 덮개가 둘러쳐 있다. 아예 사람이 손을 댈 수 없다.
정비를 할 때에도 안전 최우선이다. 현장 안내를 맡은 CJ제일제당 관계자는 불쑥 투명 덮개를 열고 몸을 설비 안쪽으로 들이밀었다. 덮개가 열리는 순간 설비는 멈춰 섰다. 김성식 CJ제일제당 환경안전팀 부장은 “최근 3년간 연평균 31억1000만원의 안전·환경 예산을 투입했다”며 “덮개를 열면 멈추는 설비도 계속해서 확충 중”이라고 전했다.
협력업체에서도 사고는 발생한 적이 없다. 30~40명 정도의 협력업체 근로자들은 주로 완성된 제품이 나오면 운반하는 일을 맡는다고 한다. 안전사고 위험이 높은 적재 업무는 로봇으로 대체했다. 커다란 로봇팔이 제품을 차곡차곡 쌓아 올린다. 로봇팔과 사람이 부딪히는 사고를 막기 위한 조치도 이뤄지고 있다. 로봇팔의 행동 반경을 따라 철제 울타리가 둘러쳐져 있다. 울타리 안으로 사람이 들어가려 하면 설비가 멈춘다. 만에 하나 있을 수 있는 ‘위험의 외주화’를 기술적으로 줄여가고 있는 것이다. 김 부장은 “향후 컨베이어 벨트 비상정지 장치도 설치할 계획”이라고 덧붙였다.
소규모 제조업 지원 늘려야
모든 제조업 시설에 이런 안전 설비가 설치되면 좋겠지만 현실은 녹록지 않다. 중소 제조업 현장까지 이를 적용하기는 쉽지 않다. CJ제일제당 공주공장처럼 안전에 투자할 여력이 없다는 게 문제다.
그러나 방법이 전혀 없는 것은 아니다. 안전보건공단은 중소 제조업 현장의 한계와 애로사항을 감안해 ‘트러블 슈팅 사업’을 펼칠 계획이다. 사고가 주로 발생하는 분야의 작업실태를 조사하고 위험을 줄이는 방안을 사업체 대신 설계해주는 사업이다. 내년에는 성형기와 산업용 로봇을 대상으로 실태 조사에 나선다. 이후 컨베이어 벨트 등으로 확대할 예정이다.
다만 컨설팅에서만 그쳐서는 안 된다는 지적이 따라붙는다. 실제 설비를 설치할 수 있도록 지원을 병행해야 한다는 것이다. 안전보건공단 관계자는 “우선은 현장 기술지도부터 시작해 추가로 안전 확보 지원방안을 찾을 것”이라고 말했다.
공주=글·사진 신준섭 기자 sman321@kmib.co.kr
GoodNews paper Ϻ(www.kmib.co.kr), , , AIн ̿