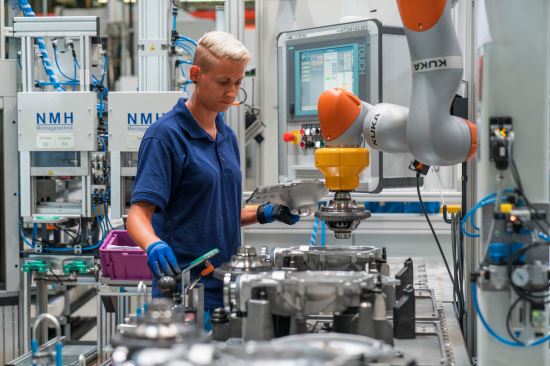
5㎡(약 1.5평) 정도의 공간에서 여직원 한 명과 ‘사버(Xaver)’가 일하고 있다. 지난달 17일 찾은 이곳은 독일 바이에른주 니더바이에른 지역에 위치한 BMW 딩골핑 공장, 자동차의 수평을 유지해주는 부품인 디퍼런셜 조립 파트다.
부품 두 개의 반쪽이 올라가 있는, 가로와 세로 길이가 각각 40㎝ 가량인 정사각형의 금속판이 컨베이어벨트를 타고 여직원 앞으로 왔다. 사버는 조립해야 하는 부품을 손에 들고 와서 30초에 한 개씩 끼웠다. 가장자리가 톱니바퀴 모양으로 생긴 두 개의 부품을 정확히 맞추고 잠시 손을 올렸다가 다음 판이 오기를 기다렸다.
공장 직원들은 이 동료 로봇에게 바이에른 지역에서 자주 볼 수 있는 이름을 지어줬다. 사버가 있기 전엔 하루에 부품 1250개를, 지금 1600개를 조립할 수 있다.
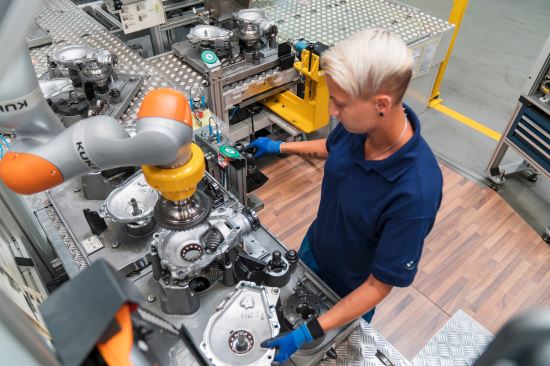
하지만 사버의 목표는 직업시간 단축보다는 작업자의 허리 보호와 부품 정밀도 향상에 있다. BMW의 사륜구동 시스템 ‘X드라이브’의 주요 부품인 디퍼런셜은 무거워서 작업자의 몸에 무리를 주고, 잡기도 쉽지 않은 형태다.
이 시스템은 5년 전 산업용 로봇 업체 쿠카(KUKA)와 함께 개발됐다. 조립 부문 책임자 베른하르트 빌은 “로봇엔 스마트 인텔리전스 프로그램이 탑재돼 있어 직원과 협업할 수 있다”면서 “사버는 직원들에게 해를 끼치지 않는다. 다만 도와줄 뿐”이라고 말했다. 작업 중인 사버의 손과 부품 사이에 빌이 손을 집어넣자 사버는 하던 일을 멈췄다.
차체 조립과 도장이 모두 이뤄지는 2.4공장으로 이동했다. BMW는 공장이 생겨난 순서에 따라 번호를 매긴다. ‘2.4’는 BMW에서 두 번째로 만든 딩골핑 공장에서 네 번째로 지어진 건물을 의미한다.
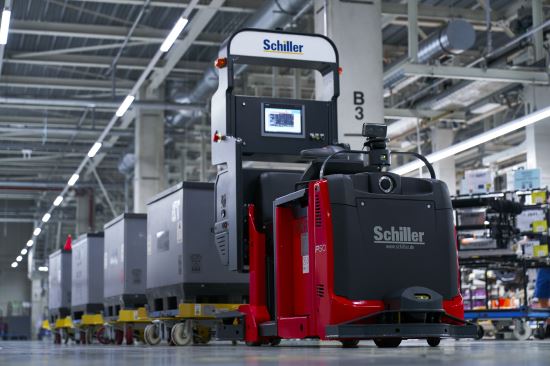
공장 2층 조립 라인과 물류 창고는 길이 300m 가량의 긴 통로로 이어져 있다. 이곳을 다니는 건 자율주행기차다. 속력은 시속 1~8㎞. 리튬이온 배터리가 탑재된 전기 무인기차다. 자율주행기차는 물류 창고에서 조립에 필요한 부품을 조립 라인으로 옮긴다. 지하철역 안내화면처럼 물류 창고 스크린에 자율주행기차 운행 정보가 나타나고, 출발 시간에 맞춰 컨베이어 벨트를 타고 오는 부품 상자가 자동으로 실린다.
스마트 물류시스템이 적용된 건 2017년. 부품을 분류하는 작업이 자동화되면서 부품을 옮기는 작업도 자동화해야 효율성을 증대시킬 수 있다는 판단에서다. 독일의 중소 시스템업체인 융 하인리히, 쉴러 등과 함께 시스템을 구축했다. 2025년까지 자율주행기차들 사이로 다니며 부품을 옮기는 소형 스마트 변신로봇도 1000대 가량 도입될 예정이다.
2.4공장의 조립 라인으로 가봤다. BMW 딩골핑 공장의 빅데이터 플랫폼(IPSi)에는 모든 부품과 도구, 조립 정보가 입력돼 있다. 덕분에 생산 시스템은 어떤 부품이 어디에 있는지, 언제 필요한지, 어디에 조립돼야 하는지 파악하고 명령을 내릴 수 있다. 예를 들어 조립 라인에 있는 5시리즈 자동차 앞부분에 나사를 끼워야한다면 작업자가 손에 든 드라이버는 차 앞부분에 위치해 있을 때만 작동을 하도록 제어된다.
이 시스템은 라인 하나에서 여러 가지 다른 자동차를 조립해도 문제가 생기지 않게 해 준다. 실제로 이날 차체 인포테인먼트 시스템을 조립하는 라인에는 BMW 3시리즈와 4시리즈, 5시리즈가 모두 있었지만 각각의 자동차에 맞는 부품을 대기시켰다가 조립하는 과정은 생산시스템이 모두 알아서 하고 있었다. 독일 스타트업 키넥슨과 함께 구축한 시스템이다.
공정을 담당하는 직원은 “빅데이터가 어떻게 활용되는지 보여주는 대표적인 예”라면서 “인간이 실수하지 않도록 도와주는 시스템”이라고 정의했다.
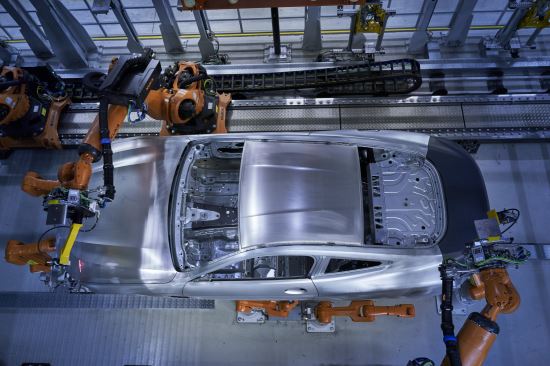
‘멀티측정소’에선 12대의 로봇이 8시리즈 컨버터블의 차체를 분석하고 있었다. 마디가 있는 긴 막대 모양의 로봇들은 끝부분에 3D 스캐너 또는 레이저 스캐너를 달고 차체를 훑었다. 표면의 광도와 라인, 디자인 완성도를 검수하는 것이다. 기존에는 한 시간에 1000개 정도 모이던 측정 테이터가 지금은 30분 안에 12만개 가량 모인다.
차체 하나는 30분이면 분석된다. 측정소 밖에서 로봇이 보내 준 데이터를 확인하던 직원은 “예전에는 직원들이 차체에 점을 찍어 각 부분을 검수한 다음 커다란 테이블에 표를 그린 종이를 펼쳐놓고 그 위에 결과를 표시했다”고 말했다.
딩골핑=임세정 기자 fish813@kmib.co.kr
GoodNews paper Ϻ(www.kmib.co.kr), , , AIн ̿